В статье рассмотрена возможность совершенствования выбора методов неразрушающего контроля для обнаружения усталостных повреждений элементов механического оборудования, находящегося в эксплуатации, с учетом свойств усталостных повреждений и реальных условий проведения контроля.
Значительное количество механического оборудования (далее — МО) долговременного пользования, различное по назначению, конструктивному и технологическому исполнению, но имеет ряд общих показателей:
✓ длительный срок эксплуатации;
✓ индивидуальный или мелкосерийный характер изготовления элементов;
✓ малую степень отработки конструкций из-за небольшого числа эксплуатируемых аналогичных изделий и ограниченной возможности проведения полномасштабных испытаний;
✓ неучтенные при проектировании воздействия, число которых возрастает со временем эксплуатации;
✓ многочисленные восстанавливающие воздействия, выполняемые по различным технологиям;
✓ большие габариты и стоимость изделий и их элементов;
✓ возможность эксплуатации аналогичных изделий в различных условиях.
Указанное оборудование является, например, составной частью гидротехнических сооружений, судов различного назначения, энергетических комплексов, технологического оборудования многих отраслей промышленности и т. д.
Из-за широкого диапазона скоростей деструктивных процессов элементов такого оборудования (коррозионное изнашивание, изнашивание трением, накапливание механических повреждений и деформаций, усталостное и коррозионно-усталостное разрушение) его техническое состояние поддерживается по системе обслуживания и ремонта по фактическому состоянию, тенденция к переходу на которую наметилась и для более типовых изделий. Составной частью таких систем является техническая диагностика, которая, в частности, решает задачу своевременного выявления эксплуатационных дефектов до достижения ими опасных значений.
Элементы таких механических систем подвергаются расчетным и нерасчетным динамическим нагрузкам, которые имеют циклический характер, что предопределяет возможность образования усталостных повреждений на отдельных участках деталей.
Возникновению и развитию их способствуют:
✓ пониженный уровень циклической прочности материала;
✓ наличие конструктивных и технологических концентраторов напряжений;
✓ воздействие циклических нагрузок, вызывающих напряжения, близкие к пределу усталости;
✓ наличие поверхностных механических повреждений;
✓ высокая и неравномерная шероховатость поверхности.
Процесс развития усталостных повреждений является длительным, в отличие от процессов образования технологических дефектов и других повреждений, появление которых связано с действием напряжений, превышающих предел прочности материала.
Усталостные трещины, как правило, образуются на поверхности, а также в зоне действия конструктивных или технологических концентраторов напряжений. Основными параметрами дефектов типа трещины являются раскрытие a (ширина), глубина h и протяженность l (длина), определяющие, с одной стороны, опасность разрушения детали и, с другой — вероятность их выявления различными методами.
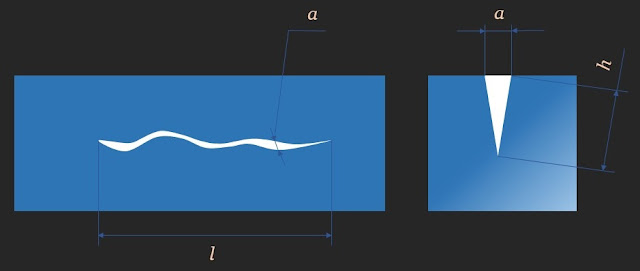 |
Классическая модель трещины |
Выполненные исследования в области усталостных трещин позволили установить их
некоторые специфические отличия.
Полости усталостных трещин во многих случаях заполнены продуктами истирания и коррозии стенок, а также смазочными материалами.
При наличии коррозионно-активной среды в устье усталостных трещин, образовавшихся в
угловых переходах, во многих случаях наблюдаются коррозионные повреждения, размер которых
значительно превышает коррозионные повреждения на цилиндрической поверхности.
По глубине усталостные трещины имеют извилистый характер, что может быть вызвано:
✓ выборочным развитием по наименее прочным участкам материала детали;
✓ изменением условий внешнего нагружения;
✓ перераспределением напряжений, обусловленных развитием трещины;
✓ влиянием соседних близко расположенных трещин, дефектов материала, полей остаточных напряжений.
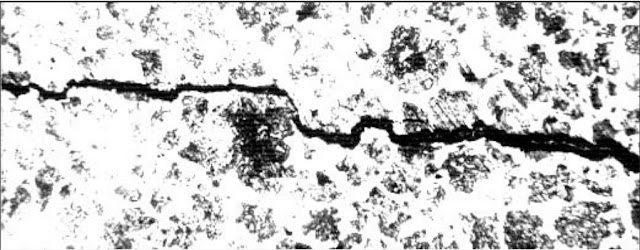 |
Усталостная трещина в средней части |
Усталостные трещины имеют переменное сечение, а также малое раскрытие по сравнению с технологическими трещинами.
Выявить усталостные повреждения на относительно раннем этапе их развития позволяют методы неразрушающего контроля, такие как ультразвуковой контроль (УЗК), магнитопорошковая дефектоскопия (МПД) — для ферромагнитных материалов, вихретоковый контроль (ВТ) и капиллярные методы контроля, далее будет рассматриваться цветная дефектоскопия (ЦД).
При эксплуатационном контроле МО возникает проблема оптимального выбора того или иного метода контроля или их комбинации, так как в нормативно-технической документации, как правило, отсутствует четкая его регламентация. Фактическая эффективность неразрушающих методов контроля (чувствительность и вероятность выявления дефектов) значительно отличается от указанных в нормативной документации на эти методы, в зависимости от характеристик дефектов и условий проведения контроля.
Рациональный выбор методов для выявления усталостных трещин может быть сделан только с учетом основных параметров реальных дефектов, их расположения и условий проведения контроля, влияние которых на чувствительность и вероятность оценивается совокупностью коэффициентов Ki , учитывающих:
✓ заполнение полости дефекта (Кп);
✓ коррозионное разрушение полости устья трещины (Кк);
✓ форму стенки трещины (Ки);
✓ переменное сечение трещины (Кс);
✓ величину размеров трещины (раскрытие, протяженность) (Кр);
✓ ориентацию трещины (Ко);
✓ геометрию контролируемого участка (Кф);
✓ нестабильность электрических (Кσ) и магнитных (К𝛍) свойств металла контролируемой детали;
✓ повышенную шероховатость контролируемой поверхности (Кr );
✓ структурную неоднородность материала (Кн);
✓ условия проведения контроля (Кт).
Значения указанных коэффициентов Кi могут изменяться от 1 (высокая вероятность выявления дефекта) до 0 (возможность допуска дефектов размерами, даже значительно превышающими приведенные в различных источниках).